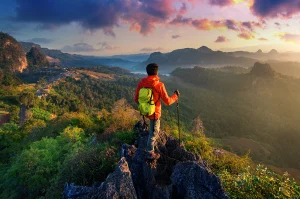
The textile industry is undergoing significant transformation due to technological advancements, particularly in the realm of digital printing. As global demand for faster, more efficient, and cost-effective production grows, digital printing has emerged as a key player in revolutionizing how designs are applied to fabrics. In contrast, traditional textile printing methods, though widely established, have limitations that digital printing seeks to overcome. This article explores the key differences between digital and traditional printing methods, highlighting the benefits, challenges, and the latest trends driving change in the textile industry.
Textile printing has a rich history, dating back to ancient times when early techniques such as block printing were used to create intricate patterns. Over the years, this evolved into more sophisticated methods, such as screen printing and rotary printing, which dominated the textile industry for decades. However, the advent of digital printing has brought a new era to textile manufacturing, offering unprecedented levels of precision, speed, and customization.
HOLDWIN, a leading high-tech digital printing company, understands the evolving needs of textile manufacturers and fashion designers. We are committed to providing innovative solutions that bridge the gap between traditional methods and the future of textile printing. In this article, we’ll compare the two approaches, offering insights into why digital printing is gaining momentum in the industry.
Screen printing, one of the most established methods in the textile industry, is known for its durability and ability to produce vibrant colors. This technique involves applying ink through a mesh screen, which is used to transfer a design onto the fabric. While screen printing is well-suited for high-volume production, it has its limitations.
Rotary printing, a modern extension of screen printing, uses cylindrical screens to print continuous patterns, making it suitable for large-scale fabric runs. While this method is faster and more efficient than traditional screen printing, it shares many of the same limitations.
Digital printing, on the other hand, represents a paradigm shift in the textile printing industry. By allowing for direct printing onto fabric using digital files, this method overcomes many of the limitations associated with traditional techniques.
Digital printing eliminates the need for creating custom screens or plates, reducing setup time and costs. Manufacturers can print designs directly from digital files, meaning that there is no need for physical screens, stencils, or molds.
Unlike traditional methods that are constrained by color limitations, digital printing allows for complex, multi-colored designs without the need for separate screens. This opens up new creative possibilities for fashion designers, allowing them to print photo-quality images and detailed patterns with ease.
One of the most significant advantages of digital printing is its ability to handle customization and small-batch runs. For textile manufacturers, this means they can print unique designs or limited-edition patterns without incurring high costs or excessive lead times.
Digital printing enables rapid production speeds. In contrast to the lengthy setup times required for traditional methods, digital printers can produce high-quality prints in a matter of hours, reducing overall production time and making it ideal for fast fashion and on-demand printing.
Digital printing is more environmentally friendly compared to traditional methods. It uses less water, generates fewer chemicals and waste, and allows for precise ink application, which results in minimal ink waste. As sustainability becomes a growing concern in the textile industry, digital printing provides a greener solution.
While digital printing offers a range of advantages, it is often perceived as being more expensive than traditional methods. However, the reality is more nuanced:
Both digital and traditional printing methods produce high-quality results, but they do so in different ways. Digital printing excels in precision and detail, especially when it comes to complex designs. The ability to print photorealistic images and subtle gradients is a clear advantage over traditional methods, which are often limited by the capabilities of the screens or plates used.
In addition, digital printing allows for better color matching and consistency across a run of prints, ensuring that each item produced is identical. Traditional methods, particularly screen printing, may suffer from color variations due to inconsistent ink application or screen wear.
As the textile industry continues to evolve, the demand for faster, more flexible, and sustainable production methods is expected to increase. Digital printing is poised to become an essential part of this transformation. At HOLDWIN, we are committed to advancing digital printing technologies to meet the unique needs of our clients. Our cutting-edge solutions, such as the foil film sublimation printer, offer textile manufacturers the ability to create vibrant, customized designs with unparalleled speed and efficiency.
By embracing digital printing, businesses can stay competitive in a rapidly changing market, offering customers a more diverse range of products while reducing environmental impact and operational costs.
“Working with HOLDWIN has completely transformed our production process. The digital printers we’ve implemented have not only cut our production time in half but have also enabled us to offer our customers more unique and personalized designs. The precision and quality are unmatched, and we’re thrilled to be part of the digital printing revolution!”
In conclusion, digital printing presents a significant leap forward for the textile industry, offering numerous advantages over traditional printing methods. From reduced costs and faster production times to endless design possibilities and environmental benefits, digital printing is reshaping the way textiles are manufactured. At HOLDWIN, we continue to push the boundaries of digital printing technology, helping businesses around the world stay ahead of the curve. By integrating these innovative solutions, textile manufacturers and fashion designers can thrive in the competitive, fast-paced global market.
Zhiyu is passionate about good products, good services, and good prices to let consumers know that choosing us is the right choice! For partners and end customers, we will provide one-on-one considerate smart services and provide you with more high-quality procurement solutions.