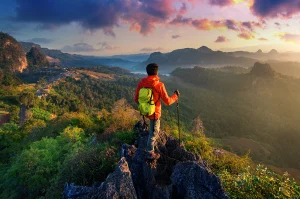
Digital printing has rapidly transformed the textile industry, enabling manufacturers to produce custom designs with minimal waste and maximum efficiency. This innovation is particularly advantageous in small-batch production, where the demand for flexibility, quick turnaround times, and customization is growing. However, despite its many benefits, digital printing presents unique challenges that need to be addressed for successful implementation. This article will explore the advantages and challenges of digital printing in small-batch production, while also highlighting how HOLDWIN, a leading brand in digital printing, can offer tailored solutions to overcome these challenges.
Small-batch production has gained popularity in various industries, particularly in fashion and textile manufacturing, due to its ability to cater to niche markets, custom orders, and rapid changes in consumer preferences. Traditional printing methods like screen printing and rotary printing often struggle with the economic inefficiencies of small runs, making digital printing the preferred choice for modern manufacturers.
Digital printing allows for the direct application of designs onto fabrics with minimal setup, making it ideal for small-batch production. Unlike traditional methods, which require the creation of physical screens or rollers, digital printing uses digital files to print designs directly onto the fabric, saving both time and cost. This capability makes it highly suitable for short production runs, custom orders, and quick product prototyping.
One of the primary advantages of digital printing is its ability to produce highly customized and personalized products. In small-batch production, this is a game-changer for industries like fashion, home décor, and promotional products. Digital printing allows designers to create unique patterns, colors, and designs without the constraints of traditional printing methods.
For example, fashion designers can print limited-edition designs or produce customized garments for customers on-demand. Similarly, promotional product manufacturers can create personalized items with intricate logos or messages, catering to the specific needs of each client.
Traditional printing methods require significant setup costs, such as the creation of screens or molds, which can make them impractical for small batches. Digital printing, on the other hand, eliminates the need for these costly setups, making it more cost-effective for smaller production volumes. This is especially beneficial for small businesses and startups that cannot afford large-scale printing operations but still want to offer unique products.
In the competitive textile industry, speed is essential. Digital printing offers a significant advantage in terms of turnaround time. Unlike traditional methods, which may require several days for setup and printing, digital printing can produce high-quality prints in a matter of hours. This quick turnaround allows manufacturers to meet tight deadlines and respond rapidly to customer demand, making it ideal for industries that require agility and speed, such as fashion and custom merchandise.
Traditional printing methods often produce excess waste due to the need for large volumes of materials, and unused ink or dye may go to waste. Digital printing minimizes this issue by printing only what is needed, reducing material waste and helping manufacturers adopt more sustainable practices. This reduction in waste makes digital printing an environmentally friendly option, which is increasingly important as sustainability becomes a growing concern in the textile industry.
With digital printing, designers have complete freedom to experiment with complex designs and gradients that would be difficult or impossible to achieve with traditional methods. This flexibility is a significant advantage in fashion and textile design, where trends change quickly, and consumers demand fresh, innovative designs. Additionally, digital printing supports variable data printing, allowing manufacturers to print different designs within the same batch, a feature that traditional printing cannot offer.
While digital printing offers several advantages, the initial cost of purchasing high-quality digital printing machines can be a significant barrier for some businesses. Although the cost of digital printing has decreased over the years, top-tier printers with advanced features, such as those used for textile printing, can still be expensive. This can be a deterrent for small businesses or manufacturers who are just starting out or are looking to transition from traditional methods.
Another challenge of digital printing is the need for ink and fabric compatibility. Digital printers require specialized inks that are designed for specific fabric types, such as sublimation inks for polyester or pigment inks for cotton. Ensuring the right combination of ink and fabric is crucial for achieving high-quality results. If the wrong ink is used on the wrong fabric, it can lead to poor print quality, color fading, or even fabric damage.
Additionally, textile manufacturers must invest in the right finishing techniques, such as heat setting or post-treatment, to ensure that the prints are durable and long-lasting. These additional steps can increase production time and cost, which may be a consideration for small-batch runs.
Although digital printing has come a long way in terms of color accuracy, it can still face challenges in achieving the same level of color consistency as traditional methods like screen printing. Variations in printer settings, ink quality, and fabric type can result in slight differences in color across batches. This may be problematic for brands that require precise color matching for their products.
For example, a fashion brand might have a specific color palette that needs to be maintained across all its products. Achieving perfect color consistency on different fabric types can be challenging, especially when working with small batches and limited production runs.
Digital printers, especially those used in textile printing, require regular maintenance to ensure optimal performance. This includes cleaning the printheads, calibrating the printers, and replacing worn-out parts. For manufacturers that are new to digital printing, understanding the technical aspects of printer maintenance can be challenging. Without proper training and expertise, technical issues may arise, leading to downtime and production delays.
At HOLDWIN, we understand these challenges and offer comprehensive training and support to ensure that our customers can operate their printers efficiently and maintain them for long-term use.
As a leader in digital printing technology, HOLDWIN is committed to providing innovative solutions that address the challenges faced by manufacturers in small-batch production. Our state-of-the-art printers, including direct-to-garment (DTG) and direct-to-film (DTF) models, are designed for flexibility, speed, and high-quality output.
We also provide personalized support and technical training to ensure that our customers can maximize the potential of their digital printing equipment. Our team works closely with customers to understand their specific needs and develop tailored solutions that optimize efficiency and quality.
“Using HOLDWIN’s digital printers has completely transformed our small-batch production process. The customization options are unparalleled, and we can now meet our customers’ demands faster than ever before. The support and training provided by HOLDWIN have been invaluable in helping us maximize the potential of our printers.”
Digital printing has proven to be a game-changer in small-batch textile production, offering numerous advantages such as cost-effectiveness, customization, speed, and reduced waste. However, manufacturers must also consider the challenges, including equipment costs, ink compatibility, and color consistency. By investing in the right technology and receiving adequate training and support, businesses can overcome these challenges and unlock the full potential of digital printing for small-batch production.
HOLDWIN is dedicated to becoming a world-renowned brand in digital printing, offering advanced solutions and personalized support that help manufacturers thrive in the rapidly evolving textile industry.
References:
Zhiyu is passionate about good products, good services, and good prices to let consumers know that choosing us is the right choice! For partners and end customers, we will provide one-on-one considerate smart services and provide you with more high-quality procurement solutions.