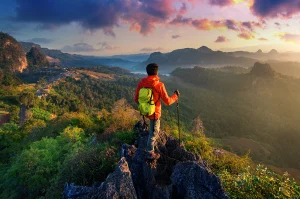
Digital textile printing has rapidly transformed the textile industry, offering significant advancements in design flexibility, speed, and cost-effectiveness. Unlike traditional methods such as screen printing or rotary printing, digital textile printing uses digital files to directly print on fabric, allowing for precise, customized designs with minimal setup. This technology has opened up exciting opportunities, particularly for fashion designers, home decor manufacturers, and businesses looking for short-run and on-demand production. However, despite its advantages, digital textile printing also faces several challenges that need to be addressed to fully realize its potential.
In this article, we will explore the key challenges and opportunities associated with digital textile printing and how companies like Shaoxing Zhiyu Digital Technology Co., Ltd. (HOLDWIN) are navigating these complexities to offer cutting-edge solutions for the textile industry.
Digital textile printing (DTP) has seen significant advancements over the past few decades. Early digital textile printers were primarily used for small, short-run prints, and while the technology was promising, it struggled to match the quality, speed, and cost-effectiveness of traditional printing methods. Over time, however, innovations in printheads, ink formulations, and fabric treatment technologies have improved digital textile printing, making it a viable option for mass production.
Today, digital textile printing is used across various sectors, from fashion to interior decor and technical textiles, thanks to its ability to produce highly detailed, colorful, and vibrant prints. The advent of new inkjet technologies, such as sublimation and direct-to-fabric (DTF) printing, has expanded the possibilities, allowing for better quality prints and faster turnaround times.
While digital textile printing has seen rapid growth, there are still several challenges that the industry must overcome to optimize the technology for mass adoption.
One of the most significant challenges in digital textile printing is the cost and performance of the inks used. Inks for digital textile printing, especially for high-quality output, can be expensive compared to traditional inks. Textile-specific inks, such as reactive dyes, sublimation inks, and pigment inks, need to be specially formulated for digital printing to achieve optimal results on various fabric types.
Another issue is the performance of inks regarding durability and washability. For applications like fashion and home textiles, the prints need to be durable, withstand repeated washes, and retain their vibrancy. Achieving this level of durability while maintaining color richness and sharpness can be a challenge with certain ink types, particularly when working with synthetic fabrics like polyester.
While digital textile printing is fast for small to medium-sized runs, it still faces challenges in terms of speed when compared to traditional methods such as screen printing or rotary printing, especially for large-volume productions. Digital printers can be slower when printing large designs or intricate patterns due to the complex nature of the printing process and the precision required for high-quality results.
In high-demand environments such as fashion and textile manufacturing, where time is a critical factor, the speed of digital textile printing can sometimes be a limiting factor. Optimizing printer throughput, improving drying times, and automating post-printing processes are key areas of focus for manufacturers looking to address this challenge.
Digital textile printing is highly versatile, but it does not work well with all types of fabrics without proper pre-treatment. For certain fabric types, especially natural fibers like cotton and wool, pre-treatment is necessary to ensure that the ink adheres correctly and produces the desired color intensity and wash fastness.
Pre-treatment processes can add time and cost to the production cycle, making it less efficient for large runs or quick-turnaround jobs. Moreover, fabrics with coatings or finishes, such as waterproof or flame-retardant fabrics, may require special handling to achieve high-quality prints, which further complicates the production process.
Maintaining color consistency across different fabrics, substrates, and printers remains a significant challenge in digital textile printing. Because digital textile printers rely on digital files to produce prints, subtle variations in color output can occur, particularly when using different printer models, ink formulations, or fabric types.
Color management is critical to ensure that the final product matches the design intent. Advanced color management systems are required to calibrate printers, monitor ink density, and ensure consistency across different print runs. However, achieving perfect color reproduction and consistency remains a challenge, particularly when working with diverse fabrics and dye types.
Although digital textile printing is often seen as a more sustainable alternative to traditional methods, it still faces environmental challenges. Ink consumption is higher in digital printing compared to traditional methods, especially when printing on large areas of fabric. Additionally, some digital inks, particularly solvent-based inks, can be harmful to the environment if not properly managed.
As the demand for more sustainable practices in the textile industry grows, there is a need for environmentally friendly ink formulations and more efficient waste management processes. Companies are investing in eco-friendly ink options, such as water-based and biodegradable inks, and exploring ways to reduce water and energy consumption in the printing process.
Despite these challenges, digital textile printing offers numerous opportunities for innovation, growth, and differentiation in the textile industry. Let’s explore the key opportunities that are driving the adoption of this technology.
One of the most exciting opportunities in digital textile printing is the ability to offer high levels of customization and personalization. Brands can create unique, one-of-a-kind prints tailored to individual customer preferences, whether it’s personalized fashion, home decor, or custom textile products. This level of personalization is particularly popular in fashion, where limited-edition designs, custom prints, and unique garment decorations are in high demand.
Digital printing allows designers to experiment with color, patterns, and textures without the limitations of traditional methods. The ability to quickly prototype and produce small batches of customized designs helps brands stay agile and responsive to changing consumer trends.
Digital textile printing is an ideal solution for short-run and on-demand production. Brands can now print only the quantity needed for a particular design or product, reducing waste and overproduction. This flexibility is especially beneficial for smaller brands, fashion designers, and start-ups, as it allows them to produce limited collections without the need for large upfront investments in screen printing or other traditional methods.
On-demand production is also more sustainable, as it reduces the need for inventory and minimizes unsold goods. With digital printing, designers can test new collections or designs without the financial risk associated with large-scale production, making it a perfect fit for fast-fashion models and small-batch productions.
As the fashion and textile industries continue to focus on sustainability, digital textile printing presents an opportunity to reduce environmental impact. Unlike traditional screen printing, which often requires large amounts of water, chemicals, and energy, digital printing uses less water and can be more energy-efficient, particularly with advances in ink technology such as water-based and UV inks.
Furthermore, the ability to print only what is needed—whether for custom designs or small batches—can significantly reduce waste in the supply chain. As consumers become more conscious of the environmental impact of their purchasing decisions, the demand for sustainable textile printing practices is likely to increase, positioning digital textile printing as a key technology in the green revolution of the textile industry.
Digital textile printing offers a significant advantage in terms of speed to market. Traditional textile printing processes can take several days or even weeks to complete, especially when it comes to creating screens or setting up production lines. Digital printing, on the other hand, allows for quick turnaround times, enabling designers to go from concept to production in a matter of hours or days.
This speed is especially important in industries like fashion, where trends can change rapidly, and brands need to respond quickly to consumer demand. By reducing the time between design and production, digital textile printing enables brands to stay ahead of trends and maintain a competitive edge.
Digital textile printing is opening up new markets and applications for the textile industry. For example, it is increasingly being used in the production of technical textiles, such as those used in medical, automotive, and industrial applications. Digital printing allows for the precise application of functional coatings, patterns, and branding, expanding the potential of textiles beyond traditional fashion and home decor markets.
Additionally, as digital textile printing technology continues to improve, it is likely that new applications and niche markets will emerge, including the use of smart textiles, wearable technology, and textiles for interactive media.
Digital textile printing represents both a challenge and an opportunity for the textile industry. While there are still challenges to overcome in terms of ink performance, speed, and environmental impact, the technology has opened up new possibilities for customization, sustainability, and on-demand production. As the industry continues to innovate and address these challenges, digital textile printing is poised to play a pivotal role in the future of fashion, home decor, and beyond.
At HOLDWIN, we are committed to advancing digital textile printing technology by providing high-performance solutions tailored to the needs of the modern textile industry. By embracing these innovations, we aim to help our clients stay ahead of the curve and meet the growing demands of a rapidly evolving market.
References:
Zhiyu is passionate about good products, good services, and good prices to let consumers know that choosing us is the right choice! For partners and end customers, we will provide one-on-one considerate smart services and provide you with more high-quality procurement solutions.