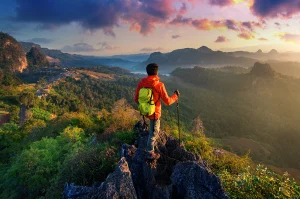
In the world of digital printing, precision and quality are paramount. The increasing demand for personalized and intricate textile designs has pushed manufacturers and technology developers to deliver consistently high standards. This article explores the essential aspects of quality control in digital printing, detailing best practices, innovative technologies, and how brands like HOLDWIN are setting benchmarks in the industry. Whether you are a textile manufacturer, a fashion designer, or a technology enthusiast, understanding quality control can significantly impact your projects and business outcomes.
Quality control is the backbone of digital printing, ensuring that every output meets or exceeds customer expectations. Unlike traditional printing methods, digital printing allows for intricate designs, vibrant colors, and rapid customization. However, these benefits can be undermined by issues like color inconsistencies, substrate incompatibility, and mechanical errors. Effective quality control mitigates these risks, ensuring seamless operations and enhancing customer satisfaction.
Maintaining accurate color reproduction is critical in digital printing. Advanced CMS tools allow operators to:
HOLDWIN’s approach includes proprietary algorithms that enhance color fidelity, ensuring that our digital prints match the designer’s vision.
Not all textiles respond uniformly to printing methods like sublimation transfer or DTF (Direct to Film). Testing each substrate ensures:
A streamlined pre-press process minimizes errors, ensuring a smooth transition from design to production. Key practices include:
HOLDWIN integrates AI-driven tools to detect anomalies before printing, saving time and resources.
Artificial intelligence is revolutionizing quality control by:
Modern digital printers come equipped with smart sensors that monitor:
Cloud platforms enable remote monitoring and control, allowing manufacturers to track production metrics and address issues promptly. HOLDWIN leverages cloud technology to provide clients with real-time insights into their printing operations.
One of HOLDWIN’s clients, a leading fashion designer, sought vibrant and durable prints for a high-profile runway collection. Using HOLDWIN’s cutting-edge digital printers and personalized support, they achieved:
The client’s testimonial reads: “HOLDWIN’s technology and expertise transformed our collection. Their commitment to quality control ensured every piece was flawless.”
As a world-renowned brand, HOLDWIN combines innovation with precision. Our state-of-the-art facilities and global perspective enable us to:
By integrating AI, IoT, and sustainable practices, HOLDWIN is redefining what’s possible in the textile printing industry.
Quality control is not just a step in the digital printing process—it is the foundation of excellence. By embracing advanced technologies, rigorous testing, and continuous innovation, manufacturers can deliver unparalleled results. HOLDWIN’s dedication to quality ensures that we remain at the forefront of the industry, helping clients worldwide achieve their creative and business goals.
Zhiyu is passionate about good products, good services, and good prices to let consumers know that choosing us is the right choice! For partners and end customers, we will provide one-on-one considerate smart services and provide you with more high-quality procurement solutions.