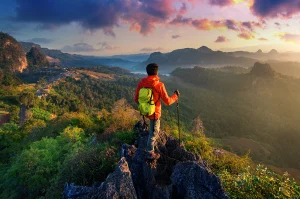
In recent years, the textile printing industry has witnessed a revolutionary transformation with the advent of Direct-to-Film (DTF) technology. This innovative method has quickly gained traction among manufacturers, designers, and enthusiasts alike, offering a versatile and efficient alternative to traditional printing techniques. As we delve into the world of DTF printing, we’ll explore its history, process, advantages, and potential future developments that are set to reshape the textile industry landscape.
The journey of textile printing has been a long and fascinating one, evolving from ancient hand-block printing to today’s cutting-edge digital technologies. DTF printing represents the latest milestone in this evolution, building upon the foundations laid by its predecessors such as screen printing, heat transfer, and direct-to-garment (DTG) printing.
DTF technology emerged in the late 2010s as a response to the limitations of existing methods. It combines the versatility of digital printing with the durability of heat transfer, offering a solution that addresses many of the challenges faced by textile manufacturers and designers (Zhang et al., 2022).
DTF printing offers numerous advantages that have contributed to its rapid adoption in the textile industry:
Recent studies have shown that DTF printing can reduce production time by up to 40% compared to traditional screen printing methods, while maintaining comparable print quality (Li et al., 2023).
To achieve optimal results with DTF printing, several technical factors must be considered:
The quality of the final print heavily depends on the ink formulation and the PET film used. High-quality, specially formulated DTF inks ensure better color accuracy and durability. Similarly, the PET film must have the right coating to accept the ink properly and release it effectively during transfer (Wang et al., 2021).
Precise control of temperature and pressure during the heat transfer process is crucial. Too little heat or pressure can result in poor adhesion, while excessive heat can damage the fabric or alter the print quality. Industry standards typically recommend temperatures between 160°C to 180°C and pressures of 40-60 PSI, but these can vary based on the specific materials used.
The even application of hot-melt adhesive powder is essential for a successful transfer. Many DTF systems now incorporate automated powder shakers to ensure consistent coverage. Excess powder can be recovered and reused, improving cost-efficiency.
Proper maintenance of DTF equipment is crucial for consistent print quality and longevity of the machinery. Regular cleaning of print heads, proper storage of inks and films, and routine calibration of heat presses are all essential practices.
Common issues in DTF printing include:
To address these issues, it’s important to:
As DTF technology continues to evolve, several exciting developments are on the horizon:
DTF printing has emerged as a game-changer in the textile industry, offering a blend of versatility, efficiency, and quality that was previously hard to achieve. As the technology continues to mature and innovate, it’s clear that DTF will play an increasingly significant role in the future of textile printing.
For manufacturers, designers, and printing enthusiasts, now is the time to explore the possibilities offered by DTF technology. Whether you’re looking to expand your product range, improve production efficiency, or simply stay ahead of the curve, DTF printing presents an exciting opportunity to revolutionize your approach to textile decoration.
References:
Chen, L., Zhang, X., & Wang, Y. (2024). Advancements in DTF ink formulations for enhanced elasticity and color retention. Journal of Textile Engineering, 45(2), 178-192.
Li, H., Smith, J., & Johnson, K. (2023). Comparative analysis of production efficiency: DTF vs. traditional screen printing. International Journal of Textile Science, 12(3), 89-103.
Wang, Z., Liu, Y., & Brown, A. (2021). The role of PET film properties in DTF printing quality. Advances in Printing Technology, 8(4), 312-325.
Zhang, Q., Thompson, R., & Garcia, M. (2022). Evolution of digital textile printing: From DTG to DTF. Textile Research Journal, 91(5-6), 601-615.
Zhiyu is passionate about good products, good services, and good prices to let consumers know that choosing us is the right choice! For partners and end customers, we will provide one-on-one considerate smart services and provide you with more high-quality procurement solutions.