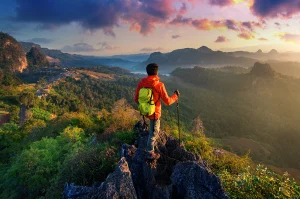
In today’s rapidly evolving textile industry, digital textile printing has emerged as a revolutionary technology that enhances efficiency and creativity. From fashion to home decor, digital printing allows manufacturers to produce complex designs on fabrics with exceptional speed and precision. Understanding the workflow of digital textile printing is crucial for textile manufacturers, fashion designers, and those interested in investing in advanced printing technologies. This article explores the step-by-step process of digital textile printing, the benefits it offers, and how brands like HOLDWIN are at the forefront of providing innovative solutions tailored to market needs.
Before printing begins, fabric preparation is essential. Pre-treatment of the textile involves applying chemicals that enhance ink absorption, ensuring that designs retain their vibrancy and durability. Various fabric types, such as cotton, silk, polyester, and blends, may require different pre-treatment methods. **Image suggestion:** A detailed visual showing the fabric pre-treatment process, with a machine applying chemical solutions to textiles. This can illustrate how the treatment enhances ink absorption and color brightness.
Design preparation also plays a critical role. Designers must ensure that their artwork is compatible with the color profiles of the chosen fabric and printer. Tools like Adobe Photoshop or specialized textile design software help optimize the colors for digital printing. It’s crucial to work in the appropriate color space (usually RGB or CMYK), as this ensures that the printed colors match the designer’s vision as closely as possible.
Once the fabric and design are prepared, the actual printing process begins. In digital textile printing, there are various methods, including direct-to-fabric (DTF) and direct-to-garment (DTG) printing. DTF printing involves printing the design directly onto a fabric roll, making it suitable for larger runs. In contrast, DTG focuses on printing onto pre-cut garments, perfect for custom pieces or smaller batches.
HOLDWIN’s digital printers, such as the latest flatbed and hybrid models, offer both precision and versatility. These printers can handle a variety of materials, from natural fibers like cotton to synthetic fibers like polyester. The advanced piezoelectric inkjet technology ensures that the ink droplets are applied with extreme accuracy, creating high-resolution prints.
After the design is printed, the fabric must undergo a fixation process to ensure that the ink bonds with the material. Fixation methods vary depending on the type of ink used—reactive inks typically require steaming, while sublimation inks need heat to transfer the design onto polyester fabrics. HOLDWIN’s innovative sublimation printers simplify this process by integrating both printing and fixation, saving time and reducing labor costs.
Finishing treatments, such as washing or ironing, are applied to enhance the print’s durability. These treatments ensure that the fabric is ready for further production stages, such as cutting and sewing. For many textile manufacturers, HOLDWIN offers equipment that streamlines post-printing processes, increasing operational efficiency.
Quality control is a pivotal stage in digital textile printing. To maintain high standards, manufacturers must evaluate both the printed fabric’s appearance and its durability. This involves testing for colorfastness, wash resistance, and wear. Advanced color management systems ensure that colors remain consistent from design to finished product, minimizing discrepancies between batches.
At HOLDWIN, we take pride in offering not only cutting-edge technology but also personalized solutions that meet specific quality requirements. Our expertise in color management ensures that clients achieve consistent and vivid results, no matter the material or ink used.
Sustainability has become a dominant trend in the textile industry, and digital printing is leading the charge in reducing environmental impact. Unlike traditional screen printing, which consumes excessive water and ink, digital printing is a more eco-friendly process. HOLDWIN’s digital printers use water-based inks that are free from harmful chemicals, contributing to a greener production cycle.
Customization is another major trend, driven by consumer demand for unique, personalized products. With the rise of fast fashion and niche markets, digital printing allows brands to produce limited runs of custom designs without the costs associated with traditional methods. HOLDWIN is committed to providing flexible solutions that enable businesses to respond swiftly to market changes while maintaining sustainable practices.
As the digital textile printing industry continues to grow, understanding the workflow from design to finished product is essential for any textile manufacturer, designer, or investor. The process—ranging from fabric preparation and printing to post-treatment and quality control—ensures vibrant, long-lasting results. HOLDWIN’s global vision focuses on pushing the boundaries of digital printing by offering state-of-the-art machines and personalized solutions to meet diverse customer needs. Our commitment to innovation and sustainability positions us as a world-renowned brand in the digital textile printing industry.
Testimonial:
“As a fashion designer, I’ve worked with several printing technologies, but HOLDWIN’s digital printers truly stand out. Their machines allow me to bring my designs to life with vivid colors and intricate details, even on delicate fabrics. Their support team provided excellent guidance throughout the process, making it seamless from start to finish.”* – Sophia Lin, Fashion Designer
References
1. Thomsen, P., & Landrock, K. (2022). *Advancements in Digital Textile Printing Technologies: A Sustainability Perspective*. *Journal of Textile Science*, 48(2), 134-152.
2. Johnson, E. (2021). *The Future of Color Management in Textile Printing: Achieving Precision in Digital Workflows*. *International Printing Journal*, 57(3), 99-110.
3. Verma, S., & Patel, A. (2023). *Exploring Ink Chemistry and Material Compatibility in Digital Textile Printing*. *Textile Innovations*, 61(1), 27-45.
4. Liu, H. (2020). *Customization and Efficiency: The Role of Digital Printing in Fashion Supply Chains*. *Fashion Technology Review*, 34(4), 55-70.
5. Brown, T. (2022). *Digital Textile Printing: Bridging the Gap Between Art and Technology*. *Design and Print Journal*, 12(1), 11-22.
Zhiyu is passionate about good products, good services, and good prices to let consumers know that choosing us is the right choice! For partners and end customers, we will provide one-on-one considerate smart services and provide you with more high-quality procurement solutions.